BMW
Spare parts DC — Dingolfing, Germany
The System at a Glance
storage locations
1000
Inther Conveyor Equipment
work stations
100
automated packing
the project
Inther Group's intralogistics optimization project in the automotive sector has elevated storage processes and production shipping dynamics for BMW, unlocking new throughput potential, ensuring timely delivery of spare parts with enhancing quality and dependability.
To meet the growing order volume and the increasing need for fast, on-time order production and delivery of spare parts, the established processes, and the existing warehouse equipment at the BMW Group site in Dingolfing, Germany have been optimized and expanded.
"A high-performance automation solution that ensures rapid supply of spare parts with enormous storage capacity, efficient processes and reliable picking quality," summarizes Inther Group Germany CEO, Stefan Weisshap.
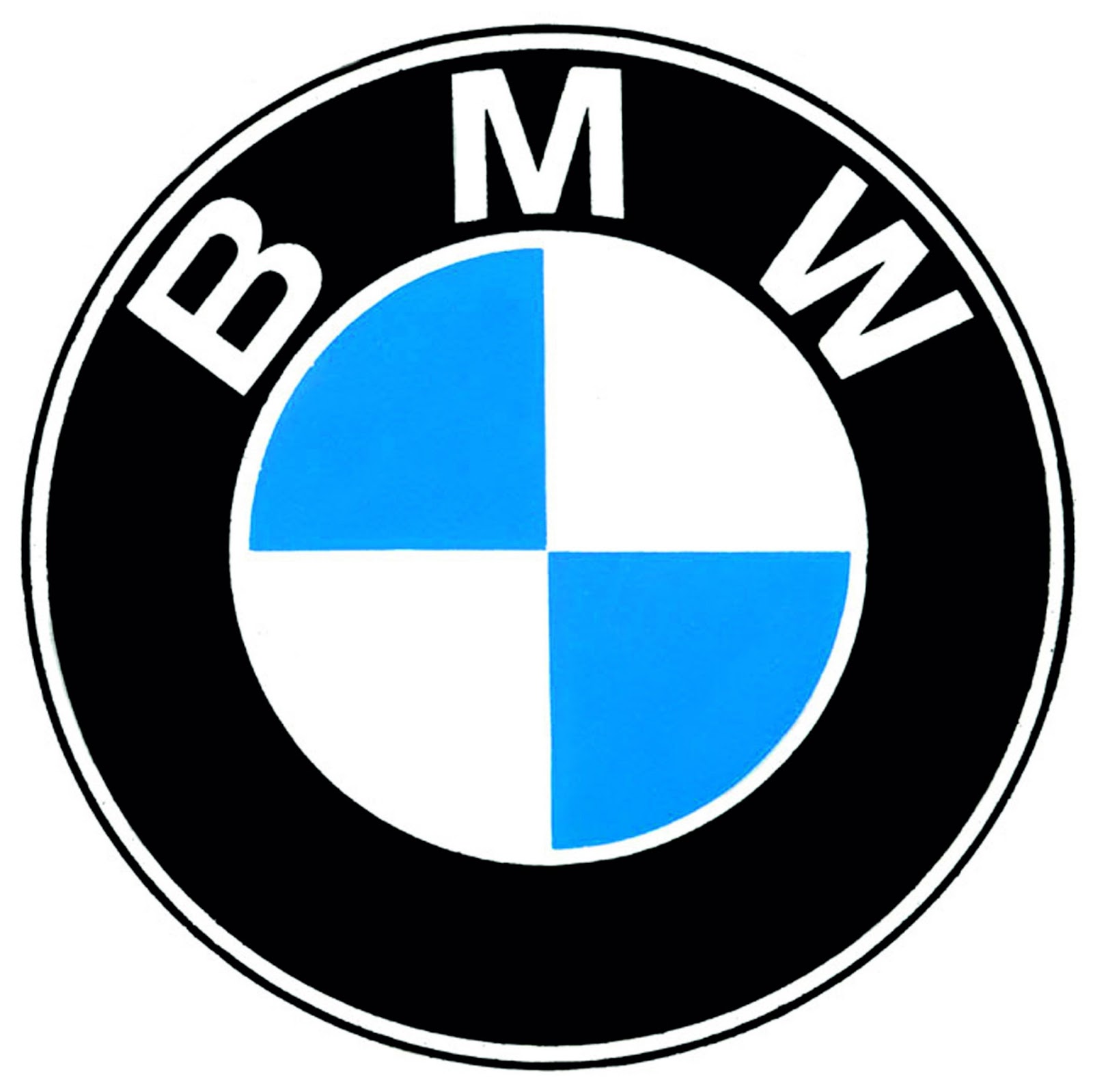
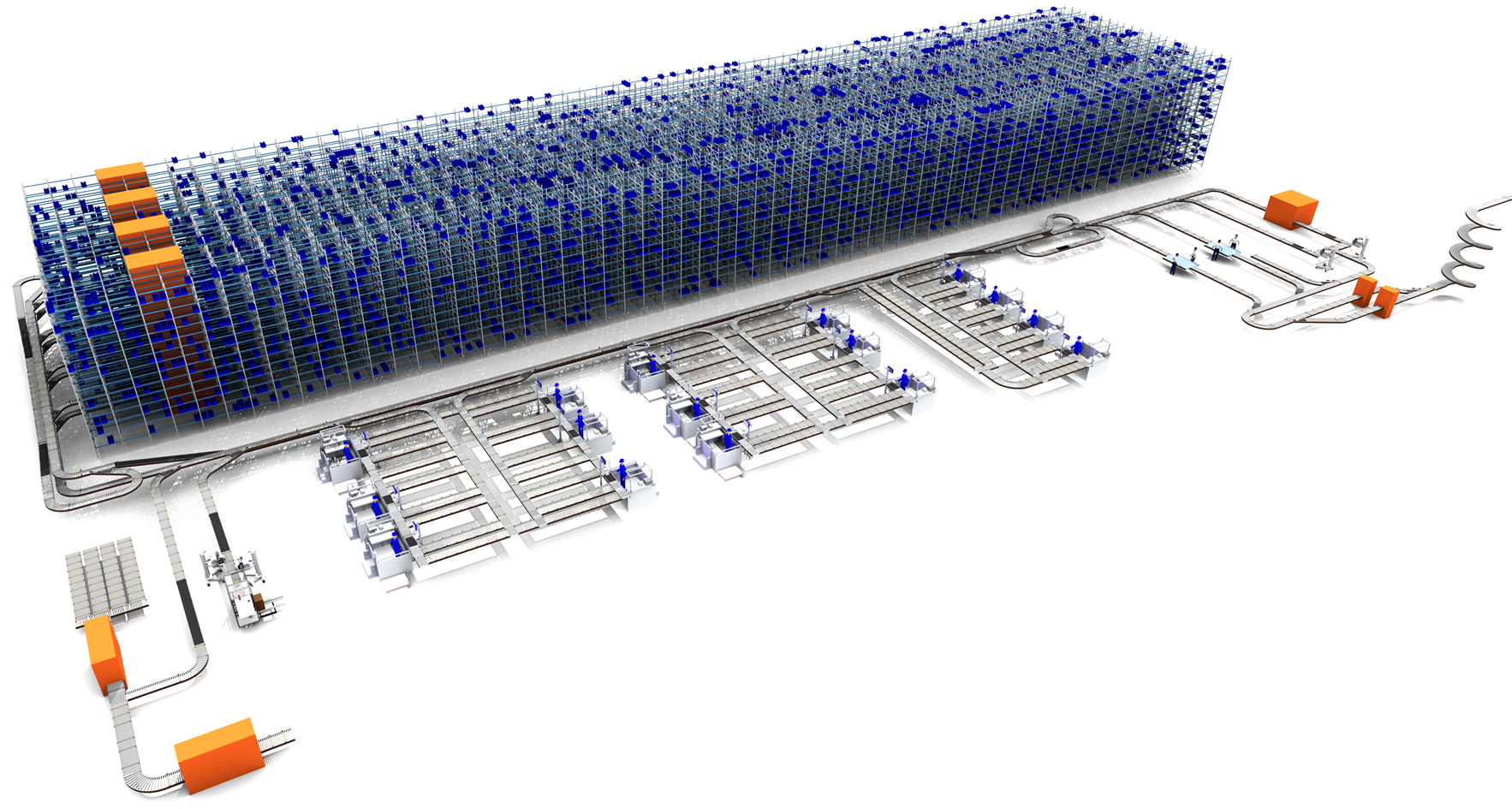
Used components
hardware Equipment
For the BMW project we used a variety of hardware solutions. Here is a list of the core components that made up our system.
Software Solutions
Inther also seamlessly connected the new automated storage and conveyor technology with the existing system technology. The visualization of the conveyor technology is done through the Zenon software, which Inther configured to meet the specific requirements at BMW. Incoming goods processing, picking, packaging, and workstation dialogs are controlled by SAP. This also applies to the shuttle system and document printing for the shipping boxes and containers.
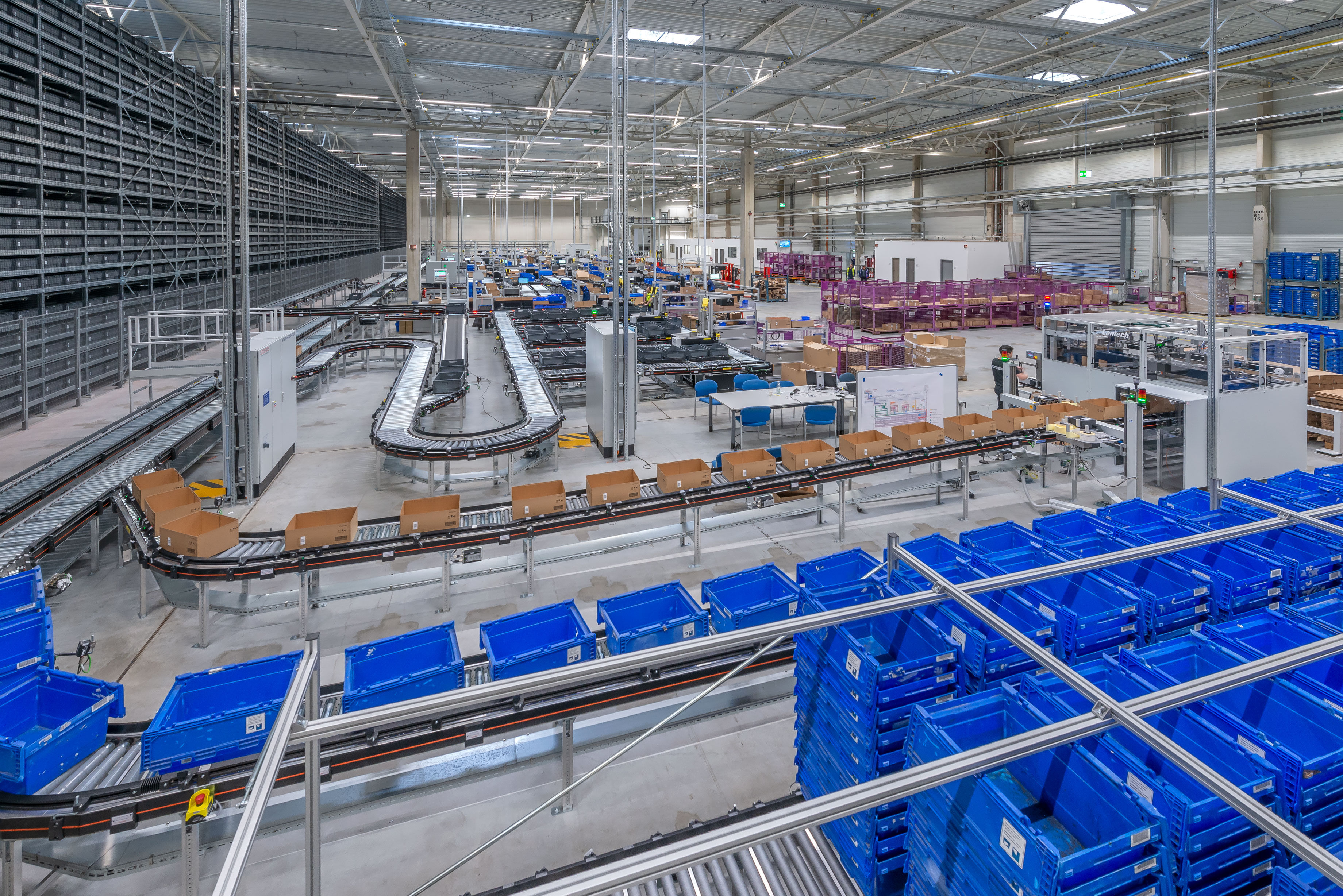