Hema
e-commerce DC - Utrecht, The Netherlands
Hema breaks records
11000m2
Surface area
130k+
Picks per day
162,5%
Capacity increase
2400/H
Shuttle totes
Hema
In four years, HEMA has increased the capacity of the e-commerce DC (from where HEMA delivers to online customers from the Netherlands, Belgium, France, Germany and the United Kingdom) from 80,000 to 130,000 picks per day. To realize this, Inther Group has largely automated the DC.
The fact that the distribution center can process so many orders is the result of a fouryear automation process. Since 2016, both storage and order picking capacity has been expanded in phases. “Until then, the operation had been set up purely manually. The only mechanization consisted of a roller conveyor, which transported the full totes from the order picking area to the packing stations”, says Jeroen Dietz, Manager E-commerce DC at HEMA.
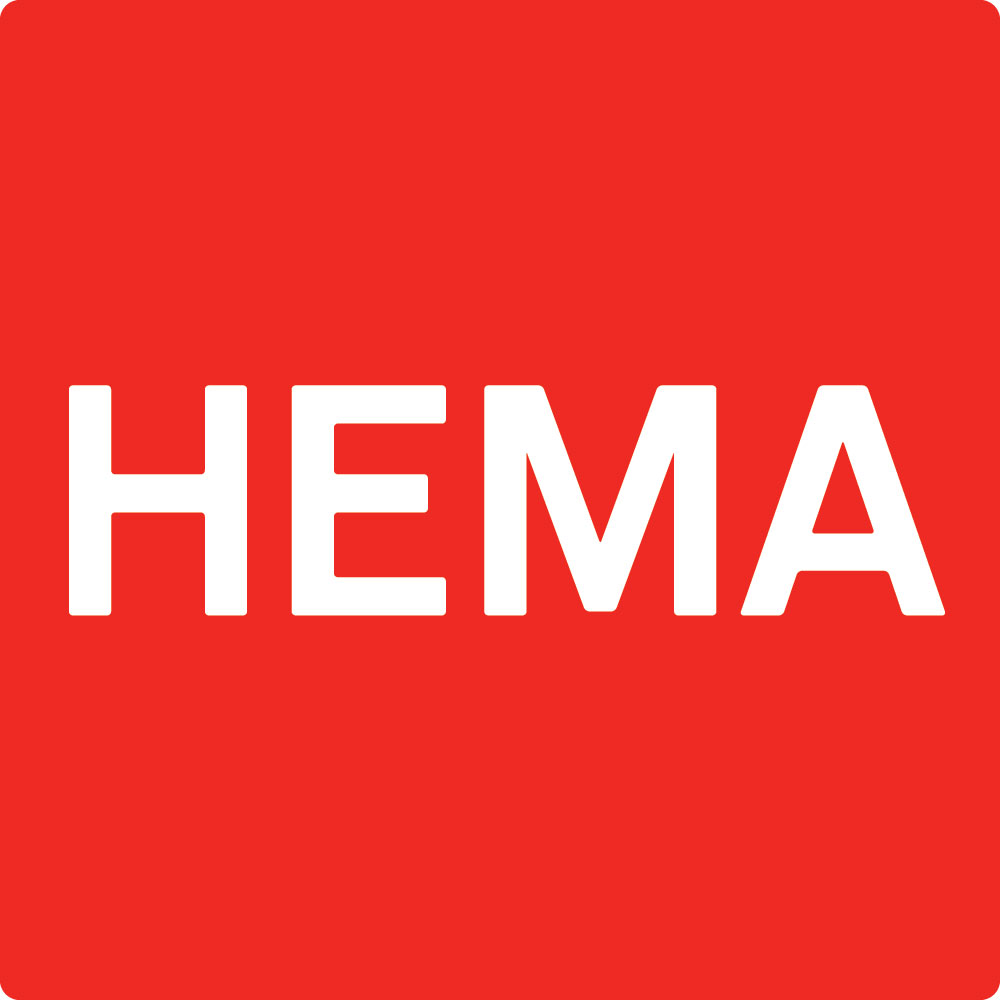
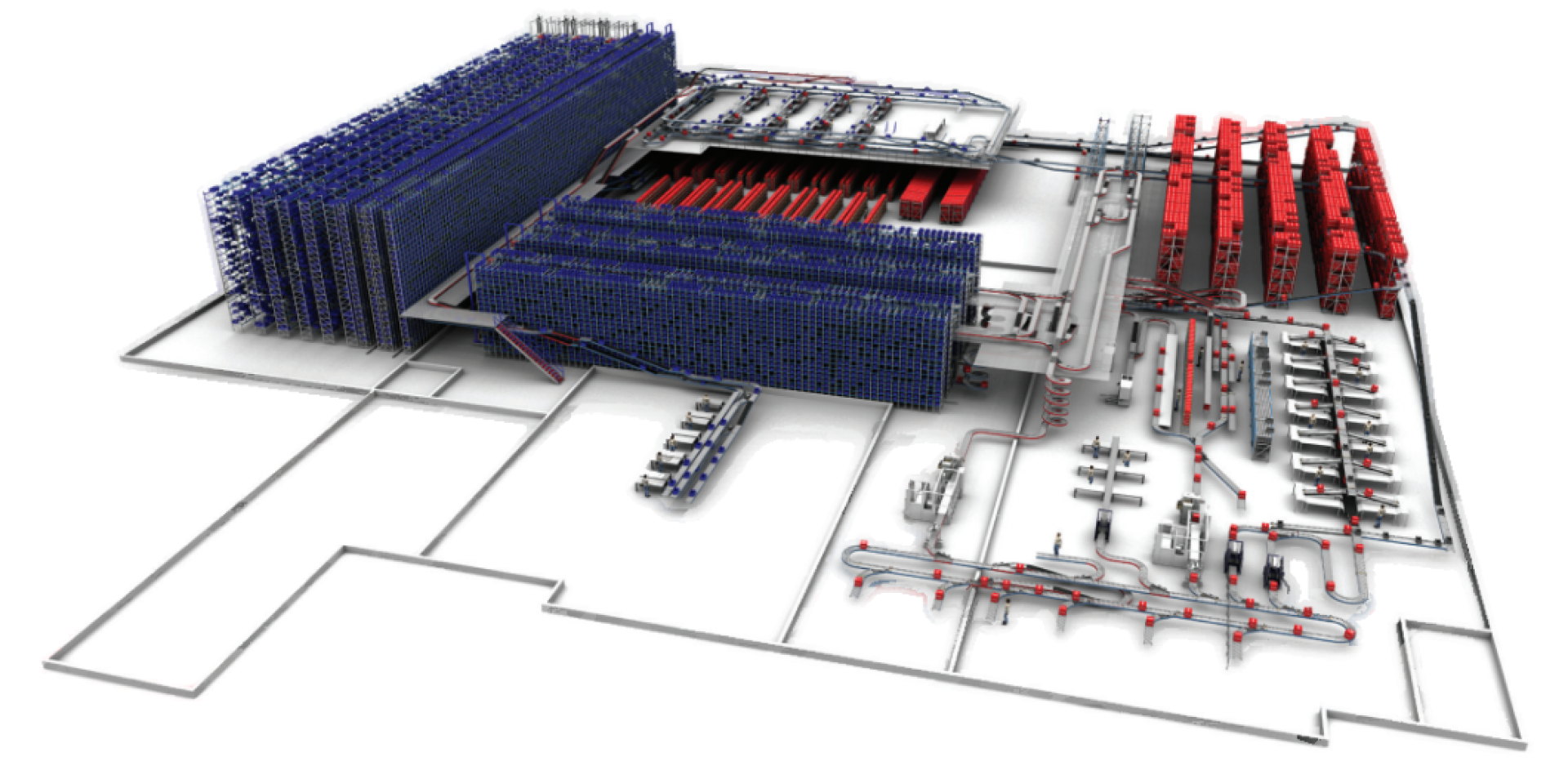
Used components
Conveyor Equipment
For the HEMA project we used a lot of self-built equipment. Here is a list of components that we used. First we start with conveyor equipment.
Miniload and shuttles
Inther was the first to install a miniload system with space for 13,000 plastic totes. This is where a large part of the bulk stock now lies for replenishment of the pick locations. The two miniload cranes place the necessary totes on a roller conveyor, which transports the new picking stock to the shelf locations. “As a result, reach truck traffi c has decreased signifi cantly. Because those reach trucks drove in the same aisles as all those order pickers with their picks, we wanted to get rid of that as quickly as possible”, Dietz explains. The following year Inther started to expand the order picking capacity. A shuttle system with space for 33,000 plastic totes has been installed for this purpose, of which 5,000 totes are divided into four compartments. The 75 shuttles, divided over three aisles, together are able to transport 2,400 totes per hour to the 8 order picking stations. There is an order picker at each station, who takes the correct number of items from the tote and distributes it to the six ready totes. “These totes contain the slow movers, which we can pick with a higher frequency than before thanks to this Goods to Person system”, Dietz says.
Full integration
Inther not only supplied the miniload and shuttle system, but also carried out the entire automation process. That also includes a box erector, label applicators, Automated Document Inserters and the conveyors that connect all machines and systems. The Warehouse Control System for integration and control of the entire system is also taken care of by Inther. “In 2016 we had to switch quickly. Inther had already supplied the pick carts and the Warehouse Management System, knew our operation from oat to barley and was able to get to work quickly”, Dietz explains the choice for Inther. In the years that followed, HEMA continued to return to Inther. “It has great advantages to bring everything under one party, so that one large integrated solution is created”, says Dietz, who is supported by Caspar de Jong, Director Global Logistics at HEMA. “With the completion of this distribution center ten years ago, we laid a foundation to which new elements were constantly added. Each addition has contributed to further optimization of the operation.”
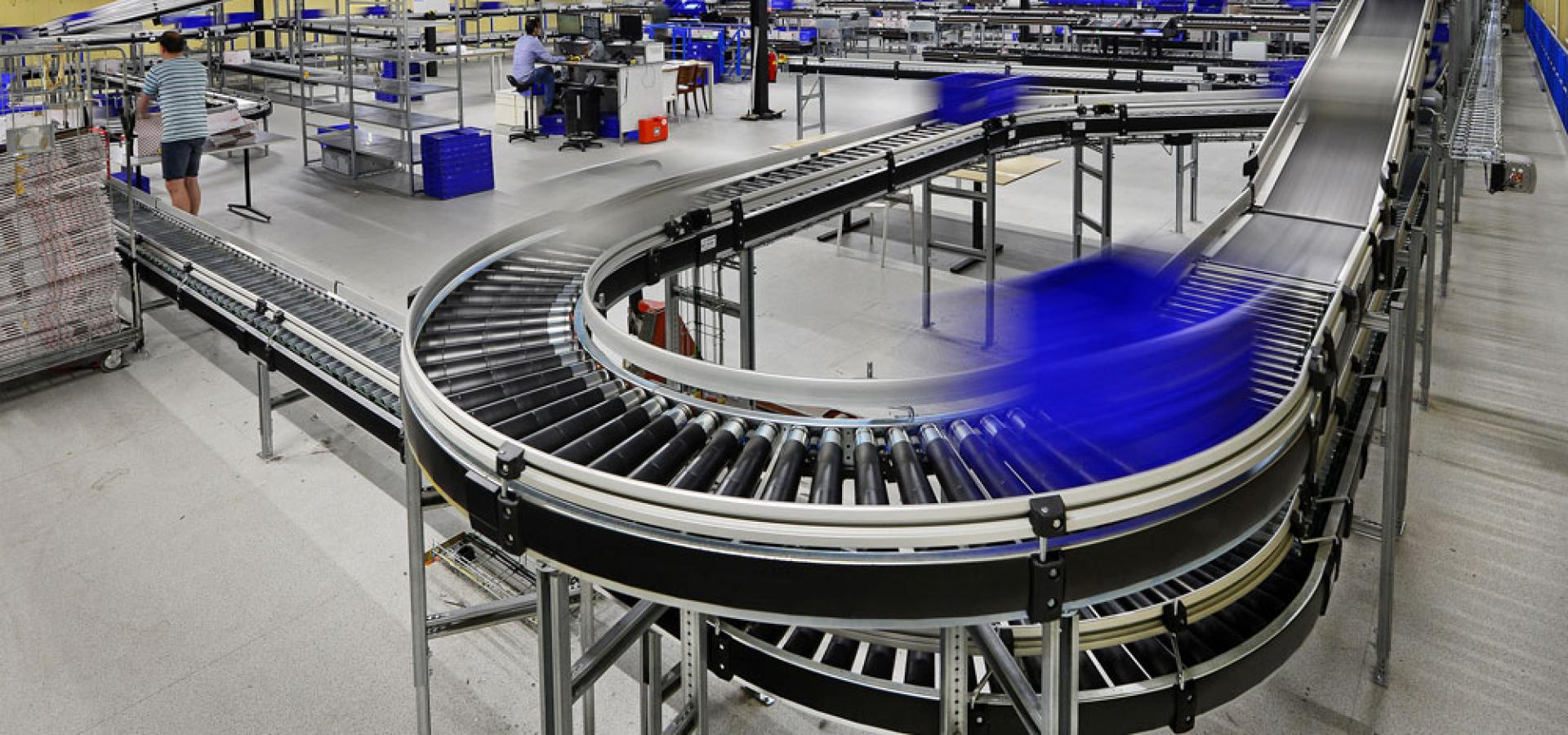